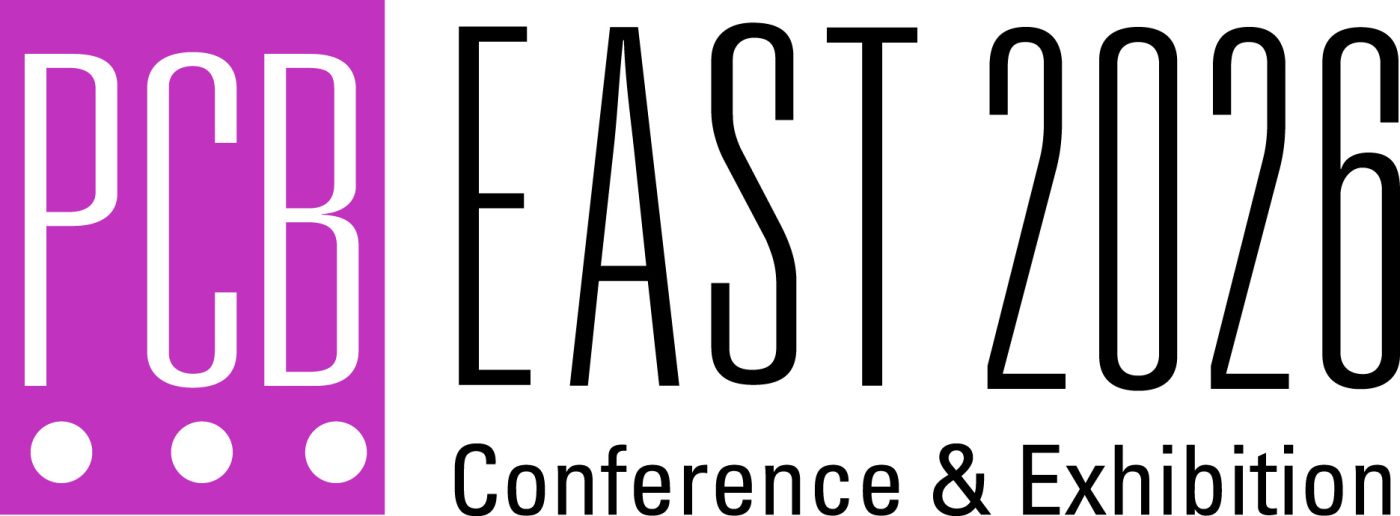
Thanks to all who participated in PCB East 2025.
Attendees and exhibitors alike were thrilled to be together and have the opportunity for learning, networking and collaborating. We’re making plans now for our 2026 event, so stay tuned!
For information on booth sales, please contact Frances Stewart (link to frances@pcea.net)